Dual Fuel Engines : Diesel – Natural Gas
Dual fuel engines can be variable or constant speed using two fuel sources, typically gasoline or diesel as the primary source. The secondary source is gaseous, such as natural gas, methane, or propane, and is blended in the air intake process. Most dual fuel engines have been converted using a retrofit kit which regulates the intake of the gaseous fuel, controls the mixing with air, and monitors engine performance to ensure the displacement from the secondary fuel does not damage the engine or negatively impact the performance of the engine. Optiblend® has installed kits on Caterpillar®, Cummins®, Kohler®, MTU, John Deere®, Mitsubishi®, and many other diesel engines.
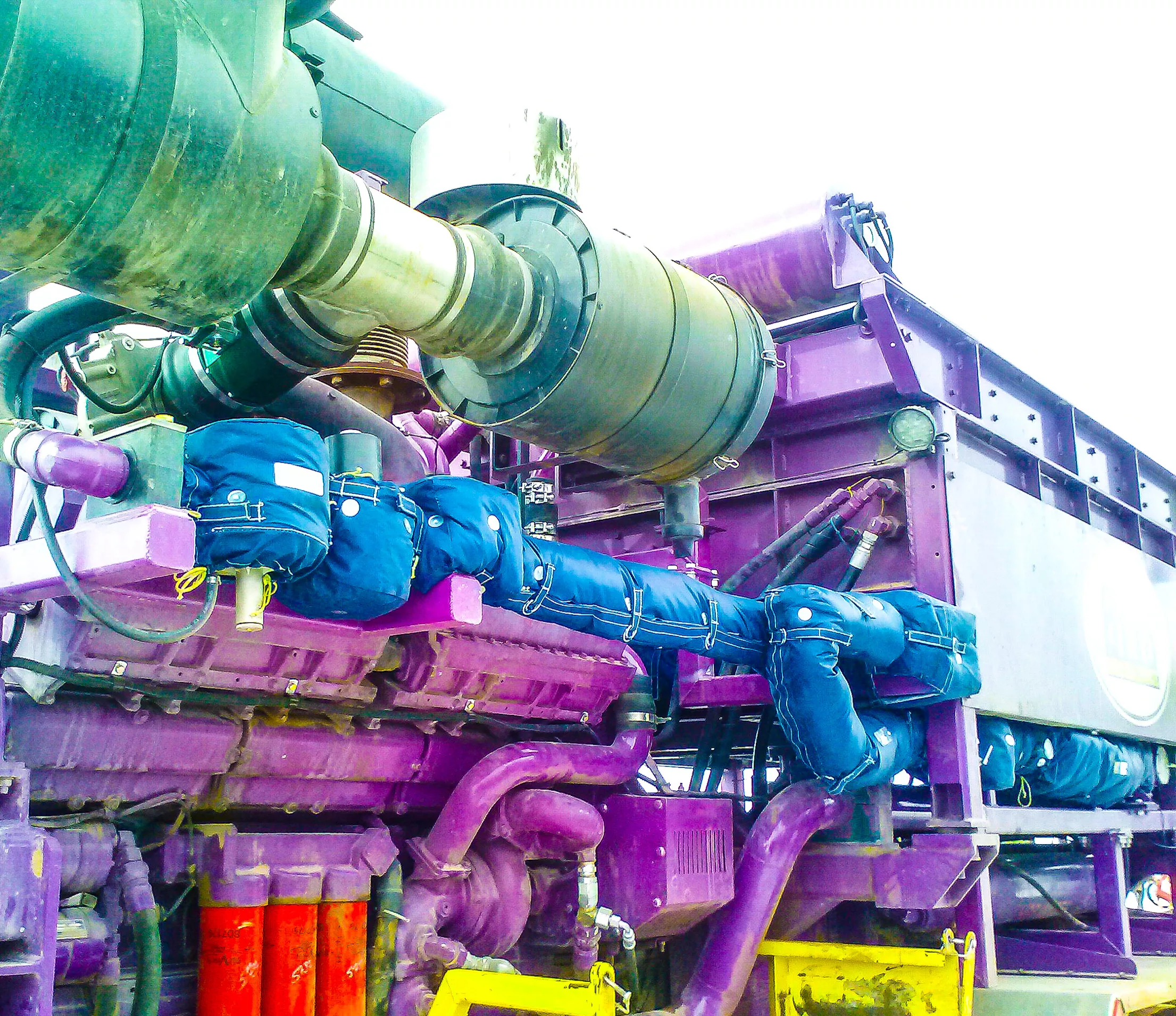
Diesel engines are used throughout the oil and gas industry to power transportation, drilling, pumping, compression, liquification, and filtering equipment required to extract, process and move high-demand raw energy resources. The cost to replace all of these engines throughout the world with newer more efficient engines would be astronomical and would disrupt the 24/7 production where minutes down are measured in tens of thousands of dollars of loss. Retrofitting diesel engines with with dual fuel conversion kits can double their runtime, save significant costs related to diesel resupply, and reduce emissions.
Caterpillar Diesel Engines Oil & Gas Operations >
Kohler Diesel Engines Oil & Gas Operations >
Dual Fuel Diesel Engines Texas Oil & Gas Operations >
Dual Fuel Diesel Engines Oklahoma Natural Gas Operations >
Dual Fuel Diesel Engines Nebraska Fracking Operations >
Dual Fuel Diesel Engines North Dakota Fracking Operations >
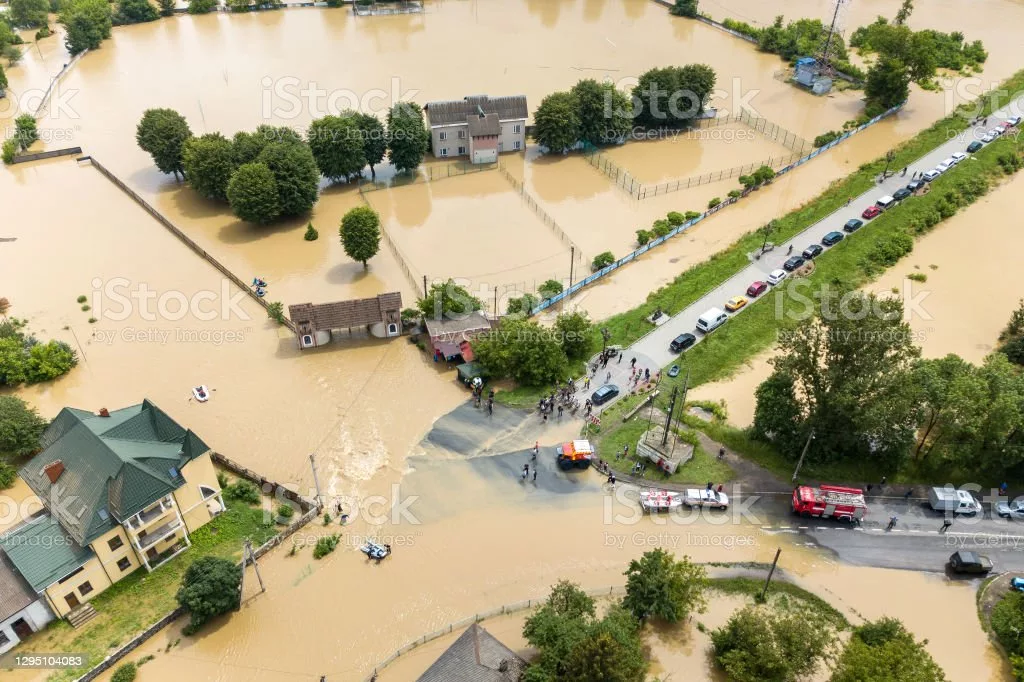
Diesel engines power first responder search and rescue, emergency medical care, temporary housing, utility restoration, road repair, structural reconstruction, and many other activities following a natural disaster. Hurricanes and floods require many millions of gallons of water to be pumped from low-lying areas. Refrigerated food and medical supplies need to remain cold. Life support systems within hospitals must continue to function to keep people alive. Retrofitting existing diesel engines allows for extended run times, lower fuel costs and reduces emissions.
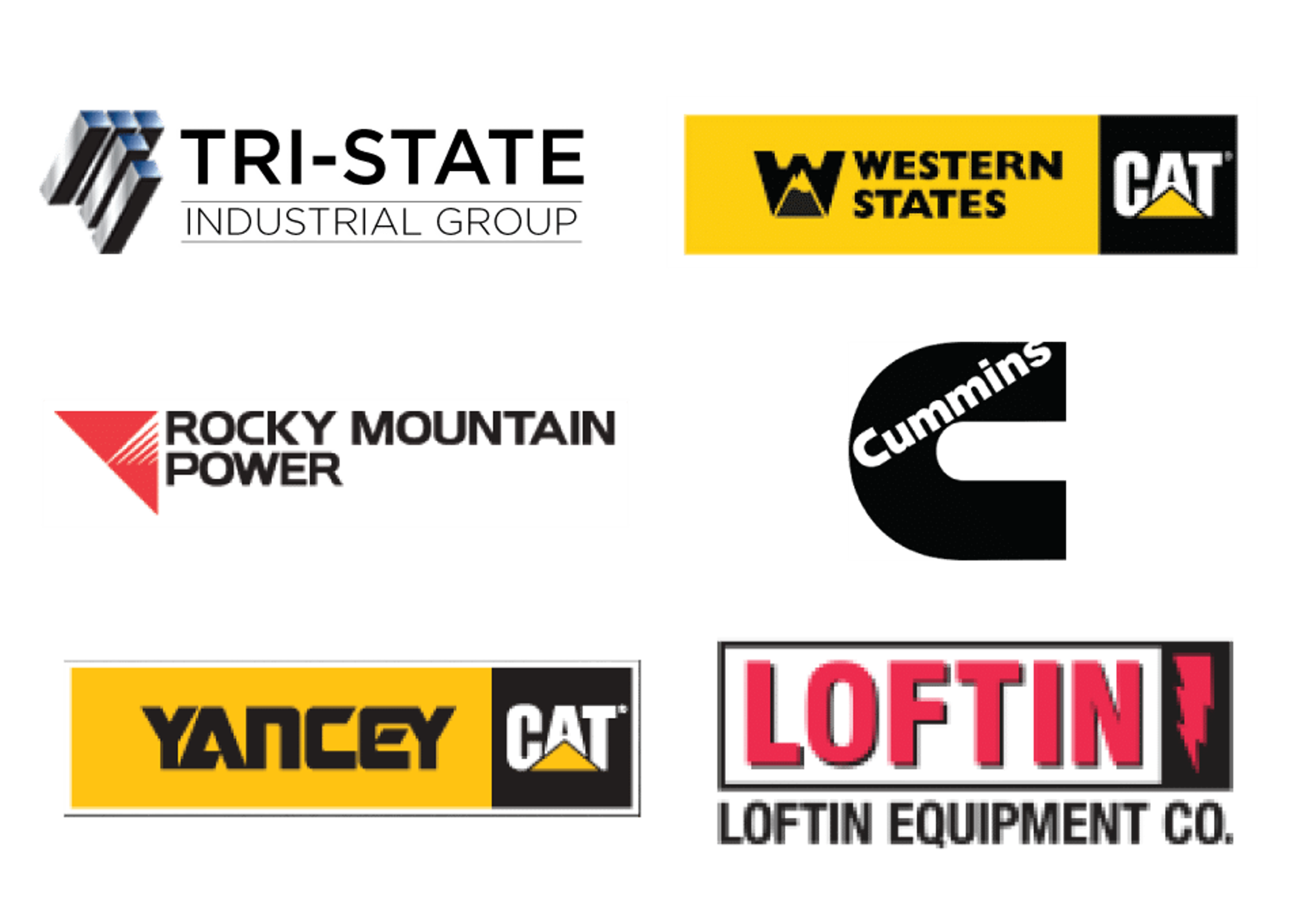
Installing a dual fuel kit onto a stationary diesel engine is easy and cost effective, displacing up to 70% of the diesel consumed. ROI can take as little as a few weeks. We have installed Optiblend® dual fuel conversion kits on Caterpillar®, Cummins®, Kohler®, MTU, John Deere®, Mitsubishi®, and many other diesel engines.
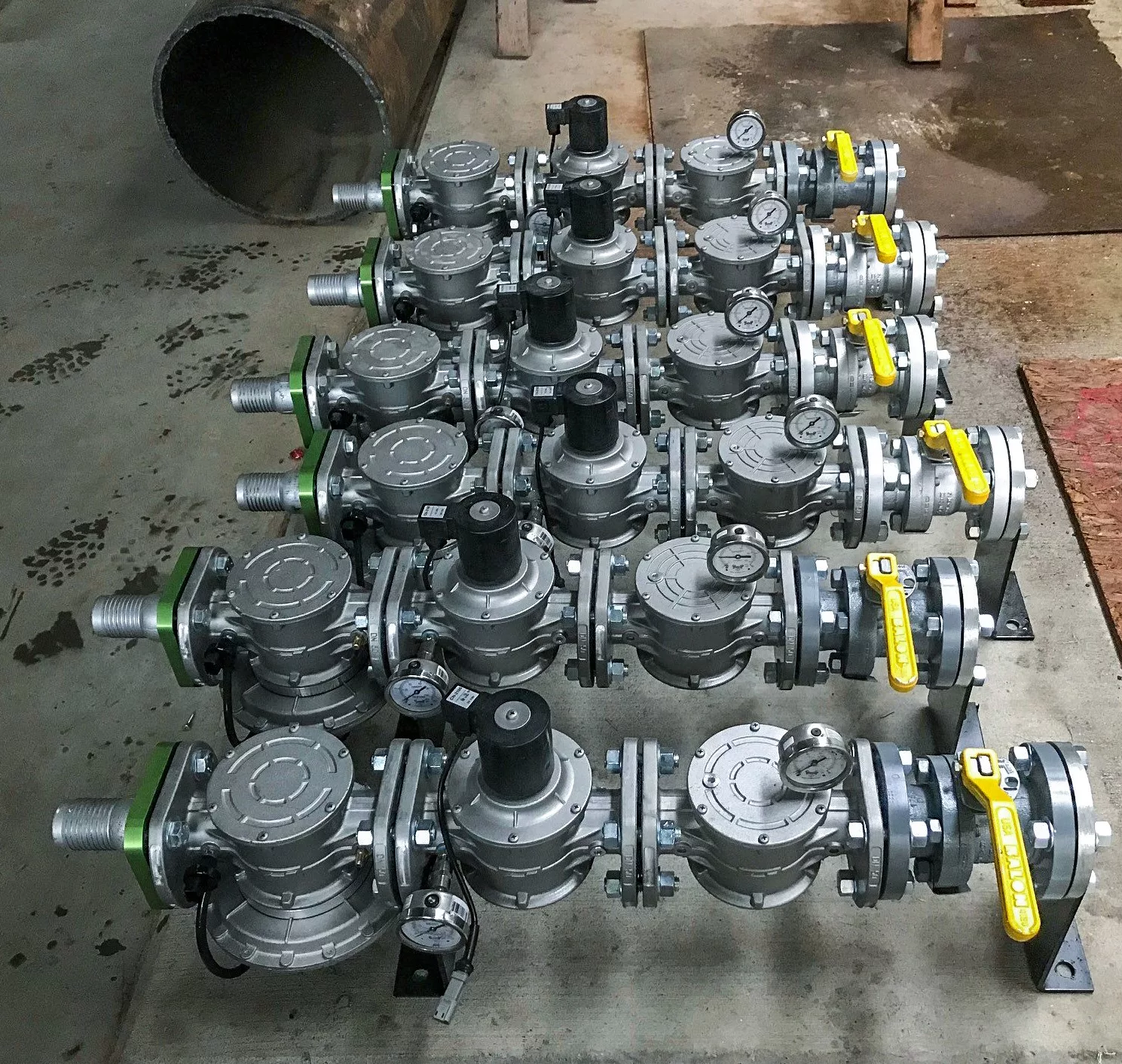
Adapting diesel engines to use a blend of diesel with compressed natural gas requires a conversion kit. A diesel engine dual fuel kit consists of a gas train, air gax mixer, fuel control valve and a controller.
The gas train uses a low pressure supply of gas (3 psi–5 psi); a primary pressure regulator can be placed ahead of the gas train to regulate high pressure supplies. A zero pressure regulator detects changes in engine vacuum through the mixer to maintain approximately atmospheric pressure and prevent over-fueling.
Contact Us
OptiBlend® in Social Media
Did you know that Optiblend can be used
Optiblend was developed using pipeline natural gas and syngas. It has also been used with propane, LNG, and biogas.
OptiBlend Dual Fuel at The Palms at Plantation, a senior living center in Florida
Last week, we successfully commissioned an MTU DS200…
Dual Fuel Generator Videos
Ready for Any Industry.
Learn why OptiBlend® is the answer to lower fuel costs, improve emissions, and increase runtime in any industry.