How it Works
OptiBlend® technology is based on the concept that inserting additional energy into the combustion chamber in the form of natural gas allows the engine to use less diesel fuel to produce the same power. The kit is a retrofit to the air intake system and does not require any modification to the engine itself or the diesel fuel management system.
Typically, 50-70 percent of the diesel fuel normally used can be safely displaced with natural gas. This greatly reduces NOx formation due to the lower combustion temperature.
If even lower emissions are desired, a partial oxidation catalyst can be added to the kit which would nearly eliminate CO and HC by products. The system was designed so that with a push of a button, you can return to diesel-only mode without interrupting engine speed or power output.
Installation of OptiBlend®
OptiBlend® Components
Gas Train
The gas train is composed of a filter, manual ball valve, lock off solenoid, and zero pressure regulator. It requires a supply gas pressure of 3 psi–5 psi. and a primary pressure regulator can be provided if your gas supply pressure is too high. The filter protects the gas train and engine from particulate contaminants which may be present in the gas stream. The gas lock off solenoid is a 24V single stage solenoid controlled by the Programmable Logic Control (PLC). The zero pressure regulator detects changes in engine vacuum through the mixer to maintain approximately atmospheric pressure and prevent over-fueling.
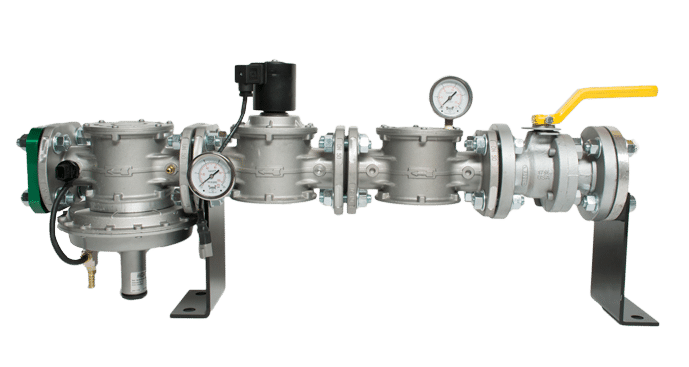
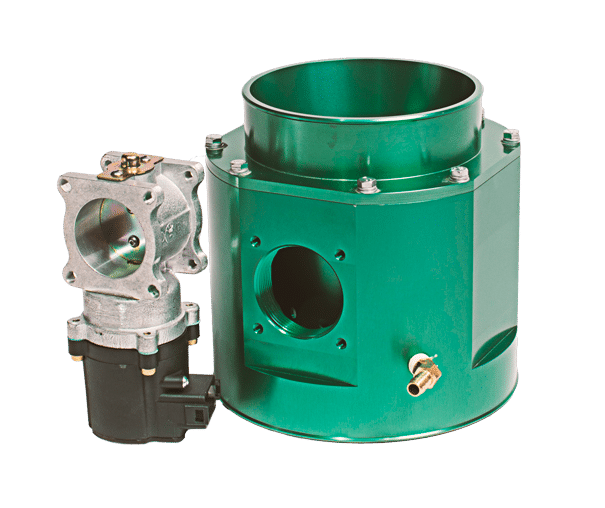
Air Gas Mixer (AGM) and Fuel Control Valve (FCV)
The Air-Gas Mixer (AGM) and Fuel Control Valve (FCV) provide for precise control of the air-to-gas ratio. The mixer design was developed by Eden Innovations LLC and will be sized specific to your engine and application. The fuel control valve has internal software with fault detection and position control with a 10–20 millisecond response time. The position is mapped versus load during commissioning and is controlled by the PLC.
Control Panel and HMI
The Programmable Logic Control (PLC) comes with two LED’s and two switches. It is housed in a fully enclosed, ruggedly designed operator terminal which is easily used with gloved hands in cold environments. The cabinet is NEMA 4X rated.
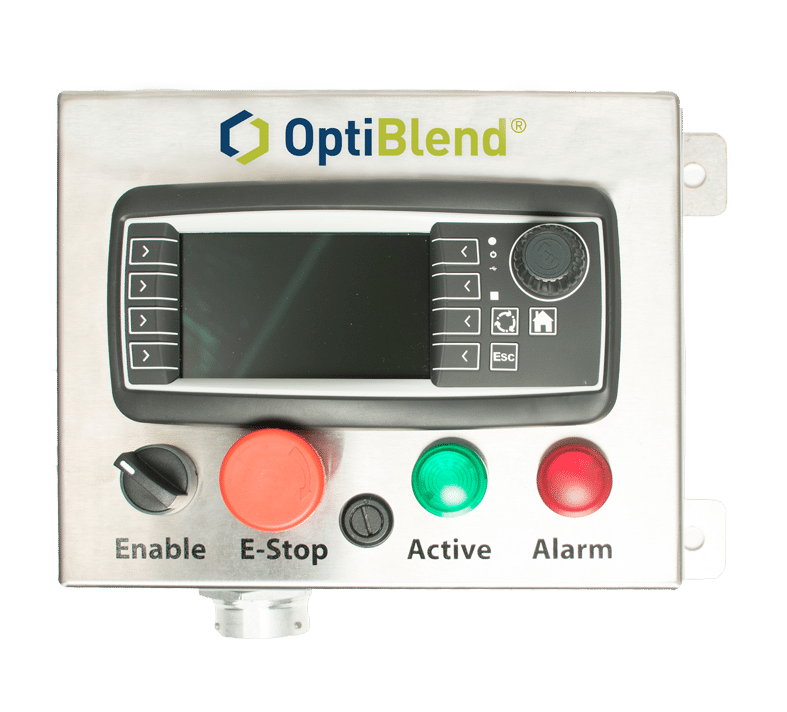
The Process
The natural gas is introduced to the air intake system through the gas train, mixer, and gas control valve. It enters the gas train from the supply line, travels through the gas train and then is delivered to the gas control valve. Here the valve regulates how much gas is introduced to the mixer. The mixer uses the Venturi effect to allow gas to be drawn into the air induction system and into the engine. This is safer than using positive pressure systems which can mistakenly allow too much gas to enter the combustion chamber, leading to engine damage.
Our proprietary control software precisely regulates the gas control valve which can adapt to engine load changes almost instantaneously. The software allows us to optimize the use of gas throughout the entire load range. Unique to the market, the OptiBlend® system can also ensure substitution rates when using variable quality inlet gas, such as unsweetened wellhead gas. Because engine parameters are constantly being monitored, engine safety is guaranteed.
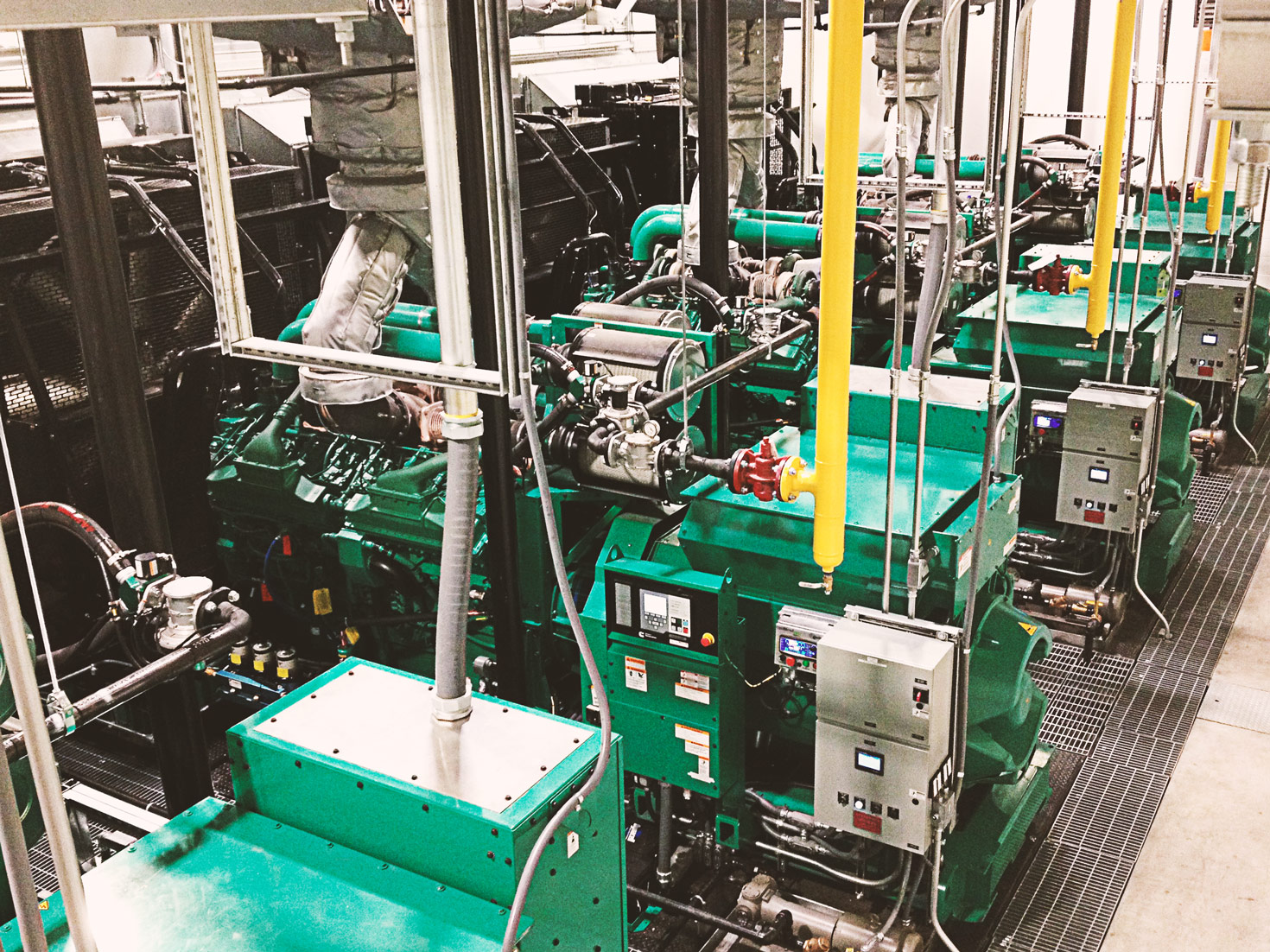
Completed Installation of OptiBlend®
Ready for Any Industry.
Learn why OptiBlend® is the answer to lower fuel costs, improve emissions, and increase runtime in any industry.